Robots speak simpler programming languages
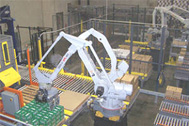
Robotics programmers can now use PAC platforms and languages they already know when deploying robots in material-handling applications.
Erik Nieves, technology director, Yaskawa Motoman Robotics
02/15/2011
Consumer-goods and food-production companies employ controls experts trained to manage complex factory-communications networks. As these companies seek wider adoption of robotics within picking, packing, and palletizing (3P)—at the expense of hard-automation lines-robots must be able to communicate easily and effectively within existing networks.
Allowing robots to take their commands from a programmable automation controller (PAC) rather than their own unique and proprietary control platform would allow robots in 3P applications to be embedded in the manufacturing controls rather than integrated to the controls.
For process-specific robotic applications, such as welding or painting, we want standard robots with their own proprietary controls and application-specific software. They exist in a larger manufacturing context and are integrated with control networks, but do their own thing for the most part. The controller firmware contains a wealth of process-specific information—for example, algorithms designed to optimize the arc-welding process to ensure smooth arc starts and minimize spatter. Internal control also keeps more processing overhead from being loaded onto the larger system.
Robots designed for these applications can be purchased with much of this process-specific programming built in, or chosen from libraries of applications. This helps get up and running faster, but such specialized programming is something of a black box to most engineers in the field who have not had specific training. They have little opportunity to understand what’s happening under the covers, but in most cases with those types of applications that isn’t really a problem.
In the consumer-goods and food-processing markets, most robots work in material-handling tasks such as assembly, packaging, and palletizing. Here, the integration process of marrying the robot controller to the rest of the workcell creates challenges and adds cost and time to the startup process.
In a recent announcement, Robotic Industries Association president Jeff Burnstein said he expects continued growth in the material-handling sector. “Material handling is important to just about every industry, and robots are reaching new users all the time,” he said.
The teams charged with installing, integrating, and managing these robots on a daily basis must have a great deal of robotics expertise. That is not a typical skill set often found in consumer-goods and food-processing plants. If the engineer overseeing the workcell does not have sufficient robotic experience, it can be difficult to optimize the installation in the context of the larger manufacturing line, and the ultimate result may never be entirely satisfactory.
For robot manufacturers to tap into that vast and growing material-handling arena, robot OEMs have two choices: Train more robot experts for these new markets, or recognize that industry is already flush with well-trained PAC experts, and leverage that knowledge base and develop technology that allows PAC/PLC experts to program and manage our robots.
Company News
- When to Automate?
Systems integrators like S&R Robot Systems help in determining how automation of - S&R Robot Systems has Moved
It is an exciting day for S&R Robot Systems. We have moved - Is Your Goal to Improve Operations, How About a Robot Palletizing System?
Eliyahu Goldraratt in his book, The Goal, stated “Productivity is meaningless unless